Behind the Building: Voxman Music Building by LMN Architects
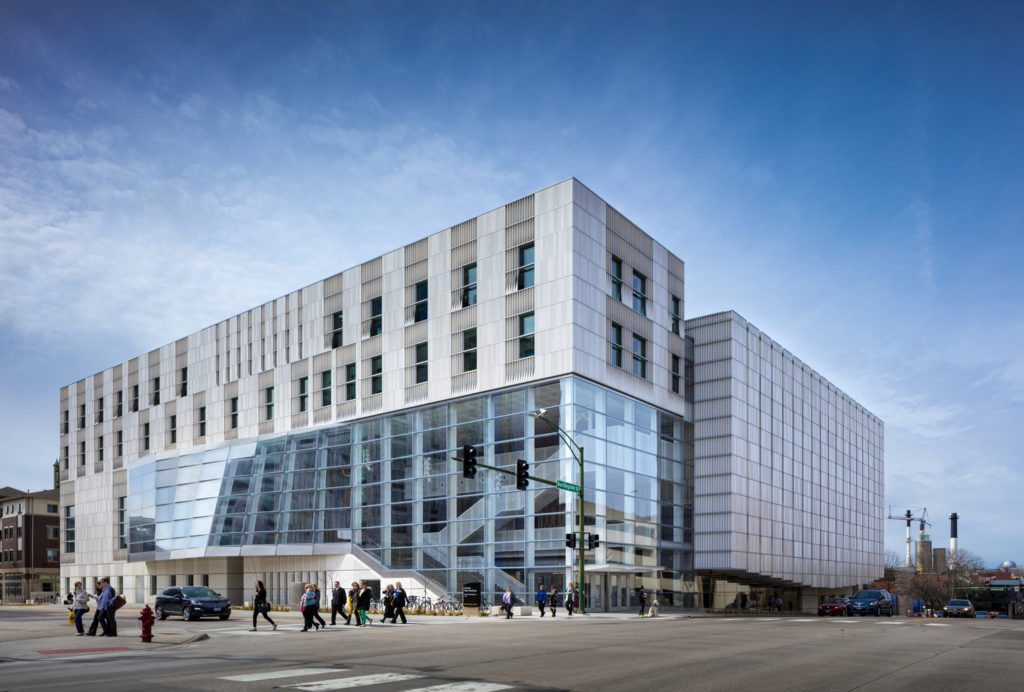
Find the perfect acoustic products for your next project through Architizer’s new community marketplace for building-products. Manufacturers: Check out the latest construction leads and sign up now.
The Voxman Music Building, designed by LMN Architects, is the latest addition to the University of Iowa’s downtown campus, replacing the former music building which was irreversibly damaged by flooding in 2008. Named in honor of the late Himie Voxman, an alumni of the school who served as its musical director for nearly three decades, the new facility was designed to “celebrate musical performance at every turn, embracing a collaborative and exploratory model of education that treats every space as performance space.”
This was no small task given the scale and diversity of the program. In total, the building encompasses 184,000 square feet of space, spread across six floors, including a 700-seat concert hall, a 200-seat recital hall, a 75-seat organ hall, a music library and Student Commons, as well as dozens of classrooms, rehearsal spaces and recording studios. The architects, working in collaboration with local firm Neumann Monson Architects and audio consultants at Jaffe Holden, designed each of these spaces with care and precision, as if crafting a musical instrument. Continue reading below to learn how every finish, from the shingled glass curtain wall to the undulating concert hall ceiling, was customized to fine-tune the building’s stellar acoustic performance.
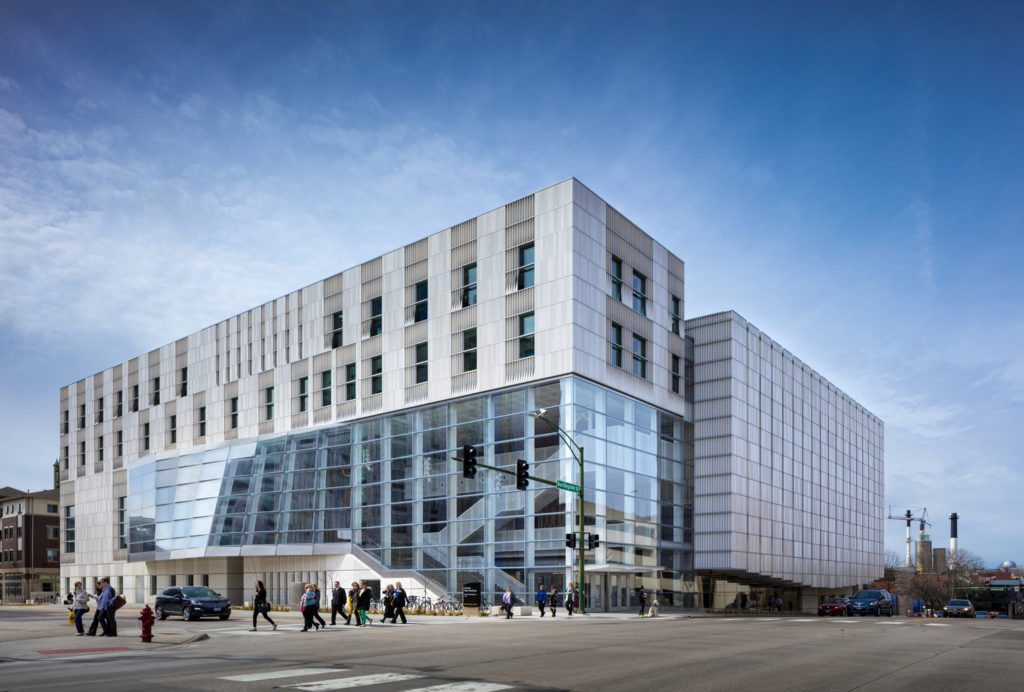
Shingled Glazing
Manufactured by Wausau and Viracon
The corner of the building is largely glazed, revealing its multi-story lobby to the surrounding city. On the second floor, the curtain wall bulges outward to accommodate the recital hall. Unlike the planar lobby façade, the glazing of the recital hall is set at various angles which reflect sound at different rates, improving interior acoustics while giving the exterior a shingled appearance.
“Due to the acoustic challenges they can present, it’s very rare to have large window views and a plentiful amount of natural light in performance and rehearsal spaces,” said project architect Stephen Van Dyck. In order to minimize the noise pollution associated with glazing, the curtain wall was specified to meet a Sound Transmission Class (STC) rating of 55. This was achieved by using two layers of 1-inch thick laminated insulating glass, separated by a 3-inch air cavity. The horizontal orientation of the glass also reduces sound distortion by stiffening it against vibrations.
Ceramic Cladding
Manufactured by Foshan X&Y
The solid portions of the building are enveloped in a custom terracotta rainscreen. The rainscreen is organized into narrow horizontal bands, like a musical score, with tiles in a variety of finishes — glazed, unglazed, smooth and grooved — creating subtle rhythms across the façade. As the architects explain, “buildings need to read at a variety of scales … At a detail scale, the shimmering quality of varied terracotta tiles becomes legible.”
At the windows of practice rooms and rehearsal spaces, the terracotta tiles seem to dance, twisting into vertical louvers which preserve views of the city while protecting students from sun glare. These 90-degree twisted tiles were the first of their kind to be used on a façade and required a year of research and development to perfect. Each was made by hand-pressing clay into curved molds and allowing it to air dry before being kiln fired.
Fabric Fins
Manufactured by FilzFelt
The building was constructed using cast-in-place concrete walls, poured extra thick for maximum acoustic isolation. However, while concrete is excellent at stopping sound transmission, it also has a tendency to produce echoes, especially when left exposed in voluminous public areas, such as the triple-height atrium and Student Commons.
This was resolved by inserting felt fins into grooves cast in the surface of the concrete. The felt absorbs extraneous noise and reduces reverberation. In addition to quieting the interior, these protruding fins lend an unexpected, tactile quality to the architecture. “It adds visual texture, gives the building a softness, and makes it more playful,” said Van Dyck.
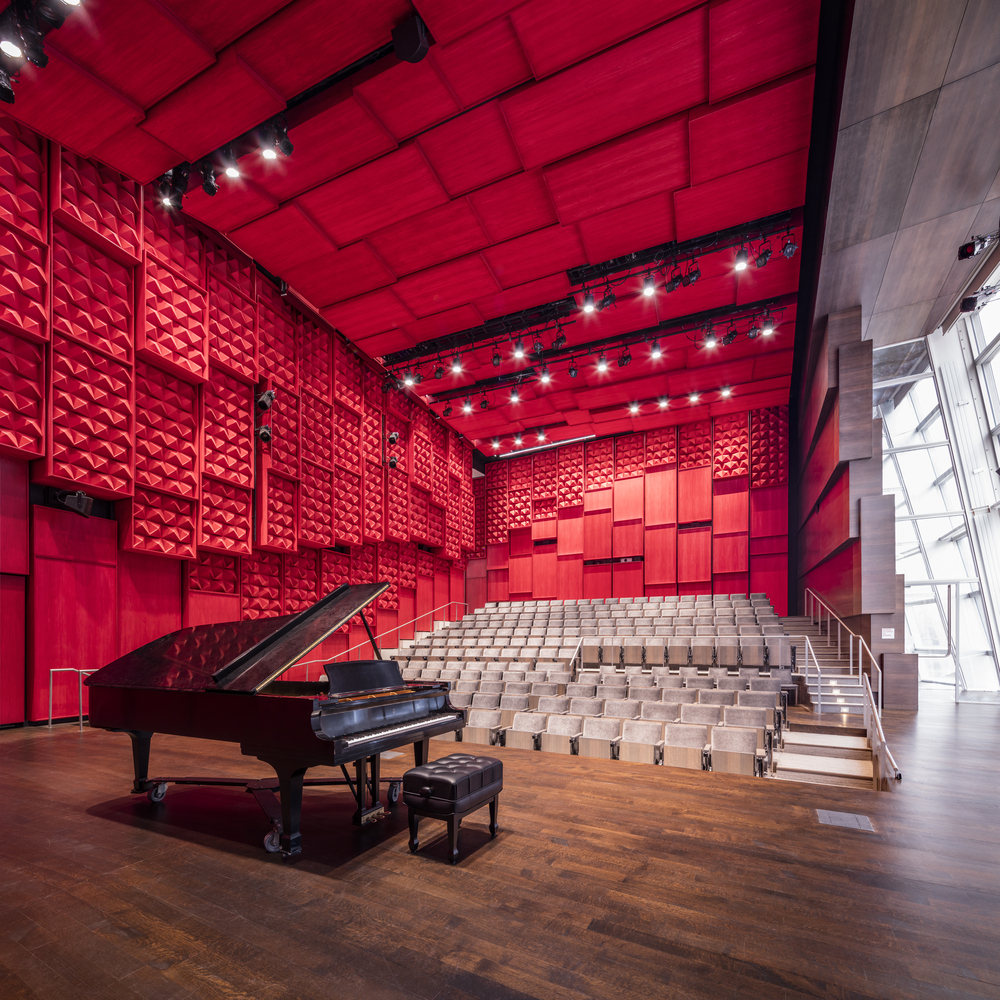
Acoustic Paneling
Manufactured by Formglas Products
In the recital hall, the gray color scheme of concrete and felt gives way to a richer expression of natural wood tones and crimson acoustic paneling. This space, nicknamed “the red room” by students, is visible through the 30-foot-tall glass façade and emits a warm glow at night, drawing attention to the performances within.
The bespoke wall panels are made of glass fiber reinforced gypsum (GFRG), cast into crystalline-like forms and painted red. Their varied surfaces diffuse sound in multiple directions for fuller, more balanced acoustics. The GFRG elements are housed in red-dyed wood frames which are staggered in depth, mimicking the shingled glazing of the curtain wall.
Suspended Ceilings
Manufactured by Alpolic and Shaffner Heaney Associates
The three main rehearsal rooms also feature bursts of color in the form of red, yellow and blue sound reflectors suspended from their ceilings. Envisioned as swarms of “kites,” these metal fixtures hover above the ensemble, accentuating the height of these spaces while directing sound back toward the musicians to create “acoustic intimacy.”
The reflectors were shaped from 36,000 square feet of aluminum using digital fabrication technology. While the solid panels diffuse sound, the perforated panels are acoustically transparent, allowing music to fill the entirety of each space. These perforations also create dynamic lighting effects, as the edges of the panels are equipped with LED uplighting.
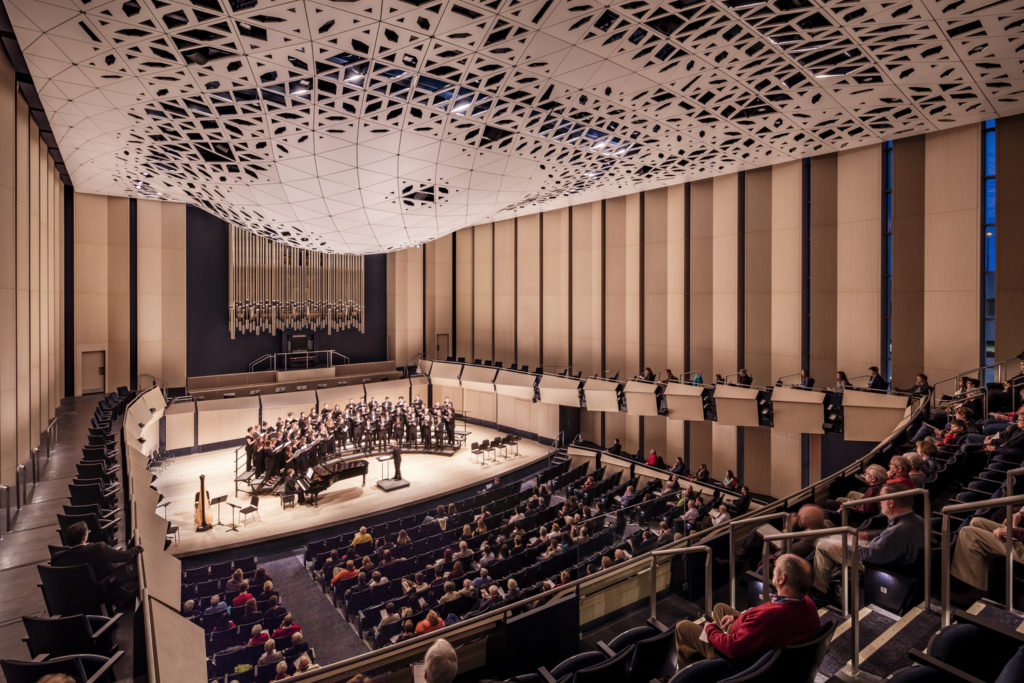
Theatroacoustic Ceiling System
Manufactured by SHApe Architectural
The playful “kites” in the rehearsal rooms foreshadow the larger, more formal ceiling in the main concert hall. Dubbed the Theatroacoustic Ceiling System, this undulant form integrates five technical systems — acoustics, stage and house lighting, fire sprinklers and audio speakers — into a single architectural element.
The curvature of the ceiling was designed using parametric modeling and raytracing software for optimal sound distribution. The model was then shared with various technical consultants who worked collaboratively to develop a pattern of perforations suited to each technical system. The finalized model was sent to a metal fabricator who cut the 946 uniquely-shaped, aluminum composite panels using a CNC-milling machine. These panels were then hand-folded and installed on a substructure of 52 curved steel ribs. The result is a one-of-a-kind ceiling, not unlike a giant snowflake, which ensures that every performance looks and sounds as good in the concert hall as in rehearsal.
All photos by Tim Griffith, courtesy LMN Architects.
Search for the best acoustic products through Architizer’s new community marketplace for building-products. Click here to sign up now. Are you a acoustic product manufacturer looking to connect with architects? Click here.
The post Behind the Building: Voxman Music Building by LMN Architects appeared first on Journal.
, Jon Cornachio, read more Journal http://bit.ly/2LL65xn
Yorumlar
Yorum Gönder