Uncontainable: The Future of Shipping Container Construction
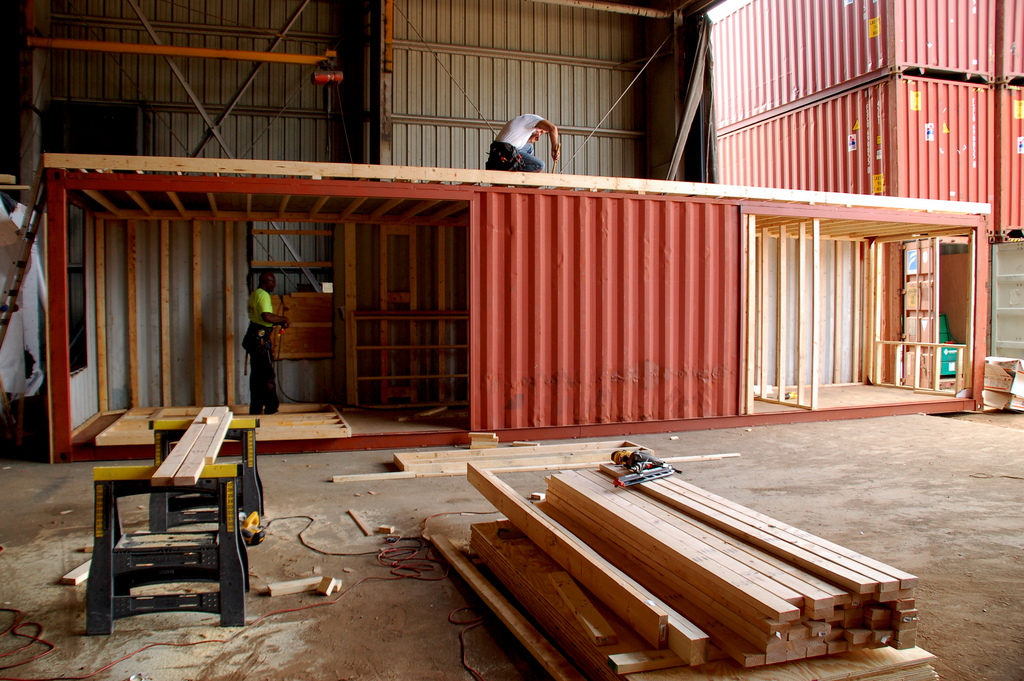
Find the perfect building-products for your next project through Architizer. Manufacturers: Check out the latest construction leads and sign up now.
SG Blocks, Inc., a leading designer, innovator and fabricator of shipping container-based structures, has signed a master services agreement with Grimshaw Architects, an award-winning, international architecture and design practice. Under the terms of the agreement, SG Blocks will incorporate Grimshaw as its premier design partner for utilization across its current projects and pipeline of future opportunities. In return, this partnership will allow Grimshaw to incorporate SG Blocks’ container-based structures into its global and award-winning industrial design portfolio.
Architizer sat down with Paul Galvin, Chairman and CEO of SG Blocks, to learn more about his company, the benefits and challenges of building with shipping containers and what this partnership with Grimshaw means for the future of the construction industry.
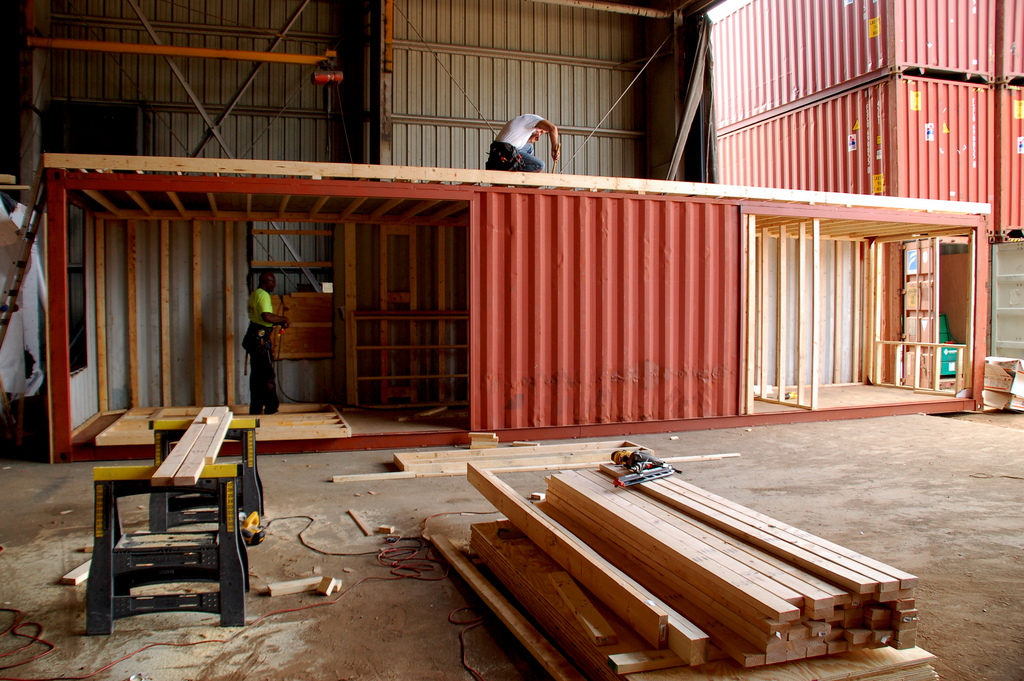
Inside the SG Blocks factory, shipping containers are modified into modular building elements. Photo via SG Blocks.
Galvin was inspired to found SG Blocks in 2007, along with businessman Steve Armstrong and former-freight ship officer David Cross, after seeing a home the pair had constructed in Charleston, South Carolina, using reclaimed shipping containers. “I immediately saw the value of this method of construction, from commercial to retail to residential,” he said, “The product especially resonated with me given my background in affordable housing and non-profit work. I saw this as an important solution to many housing problems in the U.S.”
From its inception, SG Blocks was at the forefront of container-based solutions and, last year, after nearly a decade of research and testing, the company became the first container supplier to receive an ESR number from the International Code Council (ICC). This number effectively makes SG Blocks’ containers a standardized building product, no different than a store-bought tile or mass-produced brick, which “ensures their ability to meet and exceed all international building codes” while expediting the permitting process.
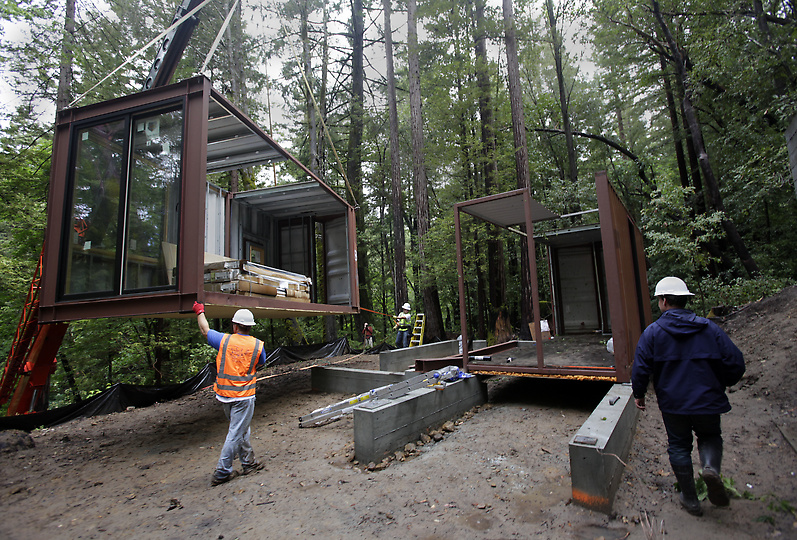
A container-based home under construction in the woods. Photo by Karen T. Borchers; via SG Blocks.
When asked the reasons to consider shipping containers over more conventional building materials, Galvin cited “better quality, efficiency, price and speed,” noting that a container-built structure can be “completed in approximately half of the amount of time and with substantial savings in most urban markets.” He went on to explain that “containers are also very durable and, since they are built to withstand maritime conditions, are hurricane and earthquake proof.”
SG Blocks is also proud of the fact that their product utilizes salvaged containers, minimizing the demand for virgin resources and reducing the ecological footprint of new buildings. Using “a recycled product is very sustainable and prefabricating modules offsite speeds up onsite construction and reduces its environmental impact,” affirmed Galvin, “Constructing your building out of a recycled building material, such as a shipping container, is also a contributor to achieving LEED certification.”
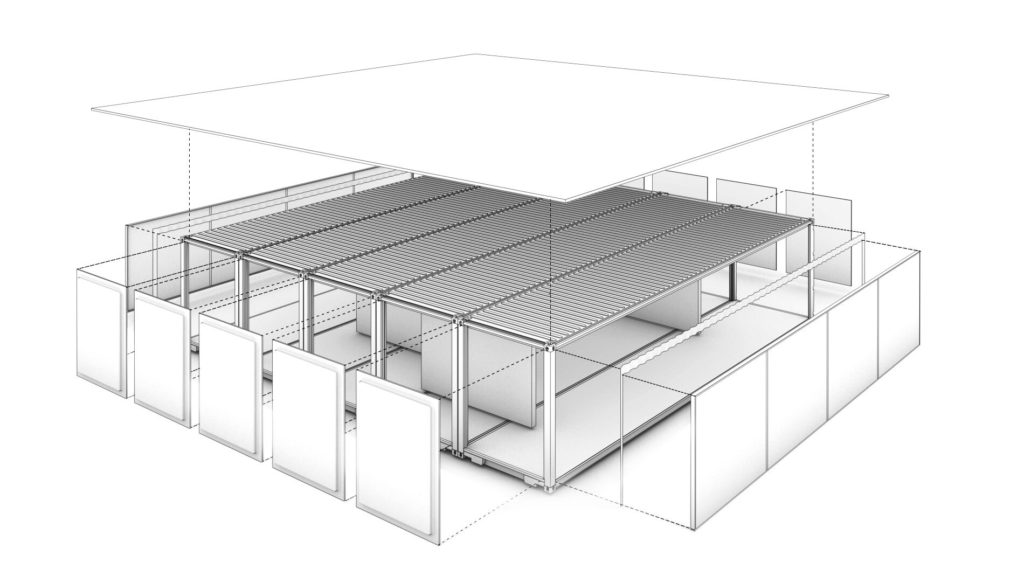
Diagram of a modular, container-based structure. Image via SG Blocks.
Despite these numerous benefits, the construction industry has been slow to adopt container-based construction, especially for large and multi-story projects. “We feel that the construction industry is protectionist and does not like new technologies because it likes to have control,” Galvin said, “But the most logical way to disrupt traditional construction is through prefabricated, modular container-based solutions.”
“The biggest misconception we face is that each room in a building is the actual size of one container. We educate people to understand that walls can be removed to create living spaces, as well as added to create rooms of any size. Shipping containers are engineered to be stackable nine stories high at sea. At SG Blocks, we maximize on this feature … We have several projects which are focused on larger-scale facilities such as a nearly 24,000-square-foot community arts and recreation center for the Heart of Los Angeles; a 6,000-square-foot retail project with Gather GVL, in Greenville, South Carolina; and an 8,000-square-foot new office space for Irontek.”
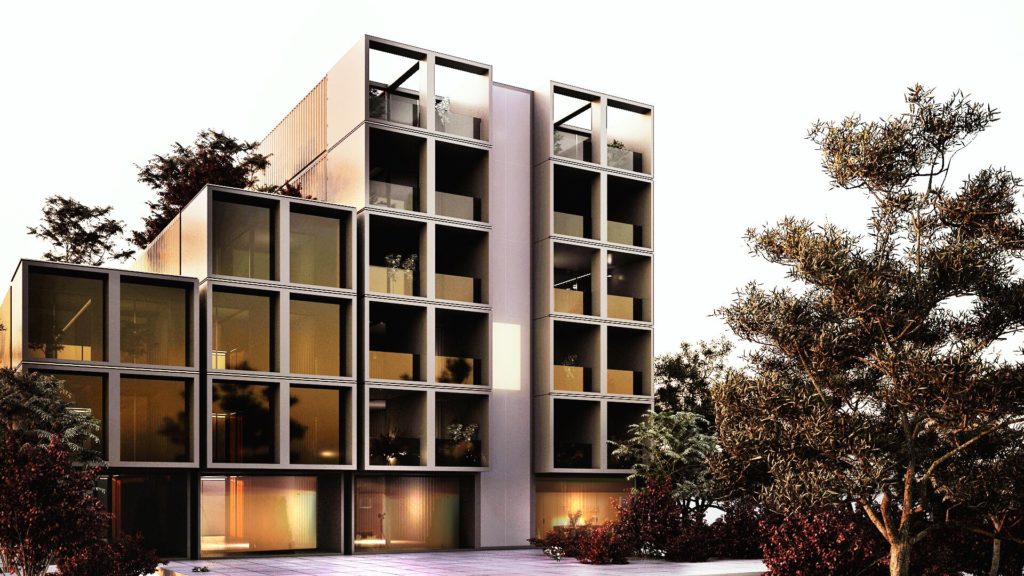
Rendering of a proposed, six-story container-built structure. Image via SG Blocks.
The newly signed master services agreement with Grimshaw Architects will help SG Blocks expand on its already impressive portfolio to bring the cost effectiveness, sustainability and customization of container-based construction to an even more diverse range of project types. “We are truly honored to be collaborating with Grimshaw, one of the premier global architectural firms in the world,” stated Galvin, “As we expand SG Blocks’ footprint both nationally and on a global scale and work on larger, more impactful projects, we look forward to working with Grimshaw to create container-based facilities of the future that set the highest possible standards of excellence.”
Search for Prefab Manufacturers
Research building-products and materials through Architizer: Click here to sign up now. Are you a product manufacturer looking to connect with architects? Click here.
The post Uncontainable: The Future of Shipping Container Construction appeared first on Journal.
, Jon Cornachio, read more Journal http://bit.ly/2mDpyol
Yorumlar
Yorum Gönder